Introduction
Photovoltaic (PV) systems have become increasingly popular as a sustainable energy solution, contributing to the global shift towards renewable energy sources. These systems consist of various components, including solar panels, inverters, mounting structures, and cables. Among these components, PV cables play a crucial role in transmitting the electricity generated by the solar panels to the inverter for conversion into usable energy. However, the exposure of PV cables to various environmental conditions, such as sunlight, moisture, and temperature fluctuations, can lead to corrosion over time. Corrosion of PV cables can compromise the efficiency and reliability of the entire solar power system. Therefore, it is essential to enhance the corrosion resistance of PV cables to ensure optimal performance and longevity of the system.
Factors Affecting PV Cable Corrosion Resistance
Several factors contribute to the corrosion of PV cables, including environmental conditions, material selection, and installation practices. Understanding these factors is crucial for developing strategies to improve the corrosion resistance of PV cables.
1. Environmental Conditions:
Environmental factors, such as exposure to sunlight, moisture, temperature variations, and pollutants, can accelerate the corrosion of PV cables. UV radiation from sunlight can degrade the outer sheath of the cables, making them more susceptible to corrosion. Moisture ingress into the cable insulation can promote the formation of corrosion-inducing electrolytes. Furthermore, temperature fluctuations can cause thermal expansion and contraction of the cables, leading to mechanical stresses that can exacerbate corrosion. Pollutants in the air, such as salt particles in coastal regions, can also contribute to corrosion by accelerating the degradation of cable materials.
2. Material Selection:
The choice of materials used in the construction of PV cables significantly influences their corrosion resistance. Common materials used in PV cables include copper conductors, insulation materials (such as polyethylene or cross-linked polyethylene), and sheathing materials (such as polyvinyl chloride or thermoplastic elastomers). The compatibility of these materials with the environmental conditions to which the cables are exposed is critical for ensuring long-term corrosion resistance. For example, using corrosion-resistant metals like tinned copper conductors can help mitigate corrosion problems. Additionally, selecting high-quality insulation and sheathing materials that are designed to withstand UV exposure and environmental stressors can enhance the overall corrosion resistance of PV cables.
3. Installation Practices:
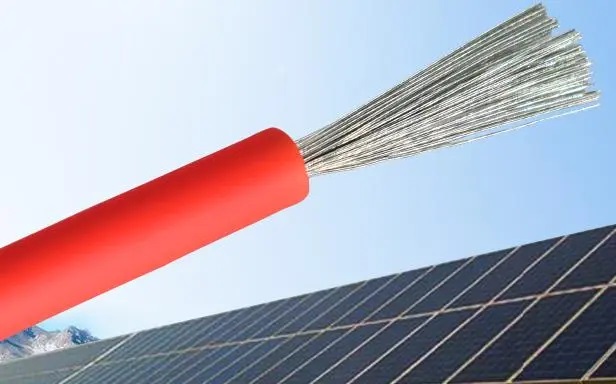
The installation of PV cables also plays a vital role in determining their corrosion resistance. Improper installation practices, such as inadequate cable support, tight bending radii, and exposure to sharp edges or abrasive surfaces, can damage the cable insulation and sheath, making them more susceptible to corrosion. Proper cable management, routing, and protection during installation can help prevent physical damage and ensure the long-term integrity of the cables. Moreover, ensuring proper grounding and bonding of the cables can help mitigate the risk of corrosion caused by stray currents and electrical faults.
Strategies to Enhance PV Cable Corrosion Resistance
To improve the corrosion resistance of PV cables and maximize the performance of solar power systems, several strategies can be implemented:
1. Use Corrosion-Resistant Materials:
Choosing high-quality, corrosion-resistant materials for PV cables is essential for enhancing their longevity and reliability. Tinned copper conductors offer better corrosion resistance compared to bare copper conductors, as the tin coating provides an additional barrier against environmental corrosive agents. Similarly, selecting insulation and sheathing materials that are specifically designed to withstand harsh environmental conditions, such as UV radiation and moisture, can help protect the cables from corrosion. Conducting thorough research on the material properties and ensuring compliance with industry standards can aid in selecting the most suitable materials for PV cable construction.
2. Implement Protective Coatings:
Applying protective coatings to the outer sheath of PV cables can provide an additional layer of defense against corrosion. UV-resistant coatings can help shield the cables from the damaging effects of sunlight exposure, while moisture-resistant coatings can prevent water ingress and the formation of corrosion-inducing electrolytes. Anti-abrasion coatings can also protect the cables from physical damage during installation and operation. Regular inspection and maintenance of the protective coatings are essential to ensure their effectiveness in preserving the corrosion resistance of the cables.
3. Enhance Cable Management and Installation:
Proper cable management and installation practices are crucial for maintaining the integrity and corrosion resistance of PV cables. Employing cable trays, conduits, and supports to secure and protect the cables from mechanical stress and environmental hazards can help prolong their service life. Avoiding sharp bends, kinks, and excessive tension during cable routing can prevent insulation damage and mitigate the risk of corrosion. Additionally, using cable glands, grommets, and sealing compounds at cable entry points can seal out moisture and contaminants, further enhancing the corrosion resistance of the cables.
4. Implement Cathodic Protection:
Cathodic protection is a proven method for preventing corrosion in metallic structures, including PV cables. By introducing a sacrificial anode or impressed current system, cathodic protection creates a protective electrical current that mitigates the corrosion of the cables. This technique is particularly effective in environments with high levels of corrosive agents, such as saltwater or industrial pollutants. useful reference and maintenance of the cathodic protection system are essential to ensure its continued effectiveness in safeguarding the PV cables against corrosion.
5. Conduct Periodic Inspections and Maintenance:
Regular inspections and maintenance of PV cables are essential for detecting early signs of corrosion and addressing potential issues before they escalate. Visual inspections can reveal visible signs of corrosion, such as discoloration, cracking, or pitting on the cable surface. Electrical testing, such as insulation resistance measurements and continuity checks, can assess the overall health and performance of the cables. Any anomalies or deterioration observed during inspections should be promptly addressed through repair or replacement to prevent further corrosion-related damage.
Case Studies and Success Stories
Several studies and real-world applications have demonstrated the effectiveness of enhancing PV cable corrosion resistance for improving solar panel performance and reliability. For example, a study conducted by researchers at a solar power plant in a coastal region found that replacing standard copper conductors with tinned copper conductors significantly reduced the incidence of corrosion-related failures in the PV cables. The use of tinned copper conductors helped mitigate the effects of saltwater exposure and UV radiation, resulting in improved long-term performance and reduced maintenance costs for the solar power plant.
In another case, a solar panel installation in a desert environment implemented protective coatings on the PV cables to combat the effects of intense sunlight and sand abrasion. The application of UV-resistant and anti-abrasion coatings helped preserve the integrity of the cables and prevent corrosion damage, ensuring uninterrupted power generation and minimizing downtime. The success of this corrosion protection strategy highlighted the importance of proactive maintenance and the use of tailored solutions to address specific environmental challenges.
Conclusion
Enhancing the corrosion resistance of PV cables is essential for ensuring the long-term performance and reliability of solar power systems. By considering factors such as environmental conditions, material selection, and installation practices, stakeholders can implement effective strategies to mitigate corrosion-related risks and optimize the efficiency of PV cables. Utilizing corrosion-resistant materials, applying protective coatings, enhancing cable management and installation, implementing cathodic protection, and conducting regular inspections and maintenance are key steps in improving the corrosion resistance of PV cables. Case studies and success stories illustrate the positive impact of these strategies in enhancing solar panel performance and longevity. By prioritizing corrosion prevention measures and adopting best practices in PV cable design and maintenance, solar power system operators can maximize their investment and contribute to a sustainable energy future.